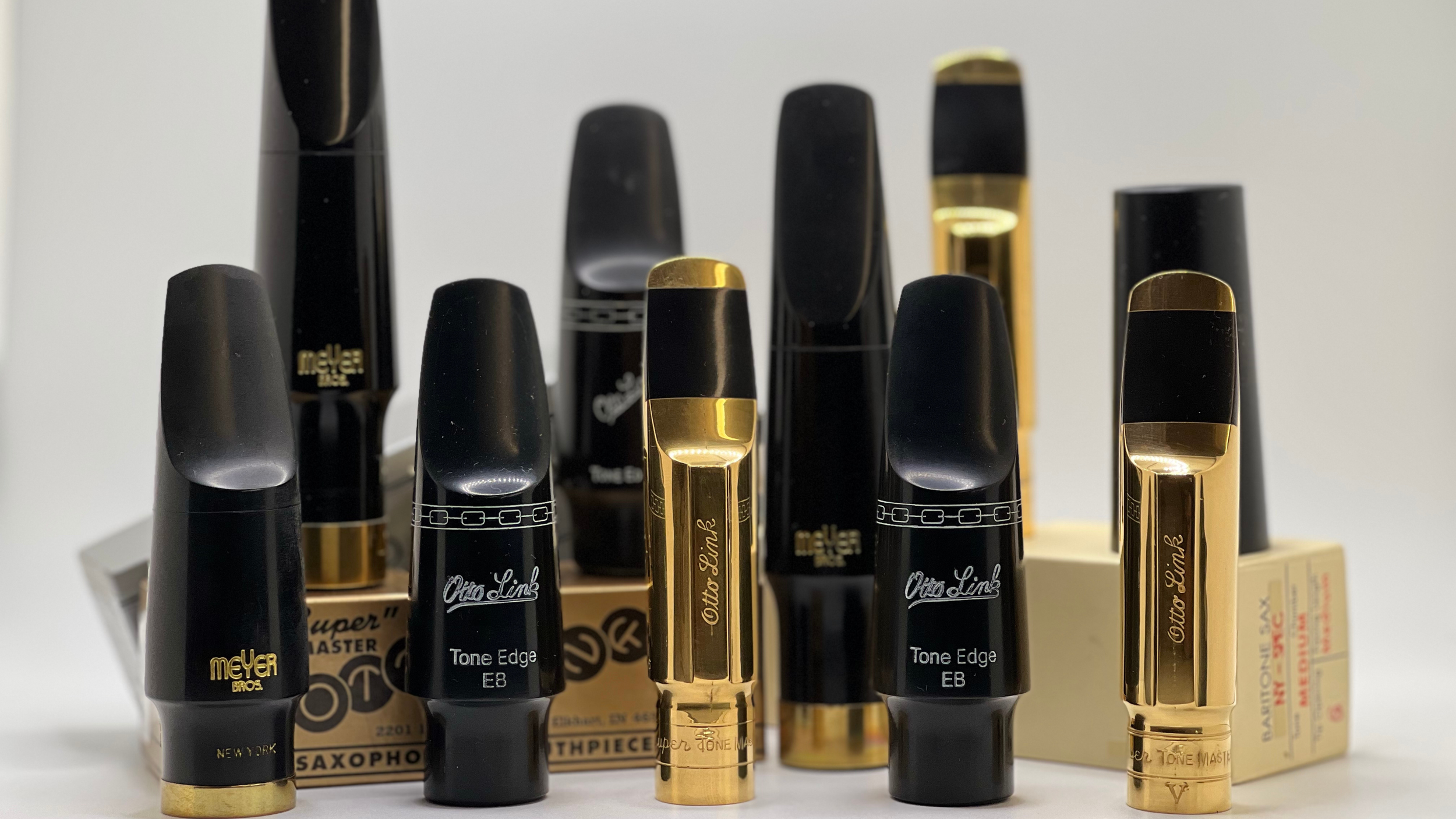
Frequently Asked Questions
We get a lot of questions here at JJ Babbitt. That tends to happen when you’ve been around as long as we have—over 100 years of crafting some of the most iconic mouthpieces in the world.
Whether you’re curious about our mouthpieces, our process, materials, or the changes we’ve made recently, we believe in being transparent and honest about who we are, where we’ve been, and where we’re headed.
Below, you’ll find answers to the most common questions we receive, and if you don’t see what you’re looking for, don’t hesitate to reach out. We’re always happy to talk shop.
-
JJ Babbitt used to be a legendary maker of mouthpieces, but now it seems like you’re nothing like what you were. The quality control has been poor for years. Why is that?
It’s a fair and honest question—and one we take seriously.
For over 100 years, JJ Babbitt earned a reputation for exceptional, handcrafted mouthpieces. But over the past 20+ years, we also earned a reputation for inconsistency. While some of the greatest mouthpieces in the world came out of our workshop during that time, the truth is that quality control and consistency weren’t always what they should have been. Truthfully, there was a great deal of organizational “drift”, and that happened for many reasons. Something not uncommon for an organization that’s been around as long as we have, but inexcusable nonetheless.
Conversations in the saxophone community often reflect this history, and we understand the specific criticisms players share—like side rails that aren’t visually consistent, tip rails with uneven thickness, and tip rails that don’t perfectly align with the reed’s curve. These concerns aren’t without merit, and we take full responsibility.
Today, JJ Babbitt is operating with a renewed purpose. Our focus is not just on producing mouthpieces but on setting a new standard—one worthy of the Meyer, Otto Link, and Hite names. Every mouthpiece we create is 100% handmade, without a single automated step. Each piece is forged, brazed, annealed, milled, mixed, molded, vulcanized, shaped, and finished by hand. This level of craftsmanship has allowed us to create some of the greatest mouthpieces in the world, but it also requires an unwavering commitment to consistency. That’s something we’ve redoubled our efforts to achieve.
Each piece now undergoes hands-on quality control at every stage, driven by the same dedication that built our reputation. Tolerances are tighter, dimensional standards are higher, and the entire process is held to new levels of rigor. While handcrafted pieces will always have slight variations—that’s the nature of artisan work—these variations should enhance, not hinder, the player’s experience.
Handcrafted mouthpieces are intentionally created with artistry and individuality in mind—not as uniform, mass-produced pieces of automation. They’re designed to resonate with the unique voice of each musician. That’s the beauty of the artisan journey. Every musician is unique, and their mouthpiece should be too—not just one of thousands of identical designs, because no player is an exact copy of another. You sound like you—and your mouthpiece should help you express that.
This renewed era of JJ Babbitt didn’t begin yesterday—it’s been in place for several years, marked by continual refinement and improvement. While we’re proud of the strides we’ve made and the pieces we’ve created during this time, our dedication to excellence means that every mouthpiece leaving our workshop today reflects the best of our heritage and the advancements we’re achieving.
But this isn’t just a change in process; it’s a change in heart. The finest tools and processes mean little without the dedication to use them with purpose and precision. Even the best resources fall short if they lack the hands and heart to wield them with true intent. That’s where our focus lies: putting everything we have into each piece, ensuring it upholds the legacy musicians have trusted for over a century.
The feedback we’re hearing from musicians about the pieces coming out of our workshop in this season has been nothing short of phenomenal. It’s clear to us we’re on the right path again, and we couldn’t be more excited about the direction we’re heading.
We honor the trust musicians place in us with every mouthpiece, knowing each piece carries a heritage of excellence. JJ Babbitt is proud of what we’re crafting today, and we believe musicians will feel the difference. We invite you to experience the renewed JJ Babbitt—a brand committed to its best self once again.
-
I've noticed a new look and feel to JJ Babbitt recently. What’s behind the change? Is it all just "marketing fluff"?
Since Steve Rorie, a 50+ year music industry veteran, took ownership of JJ Babbitt in 2021, and his son Trace Rorie became President in 2023, the company has undergone significant brand revitalization—a process that continues today. Musicians may have noticed a fresh look, feel, voice, and vibe, signaling the start of a new chapter. While honoring our legacy, we’ve long recognized the need to evolve, and we’re excited to write the next chapter.
Modern marketing—updated graphics, compelling copy, dynamic video content, building relationships with artists and musicians, and intentional social media engagement—helps tell our story. But without exceptional mouthpiece quality, all of that would ring hollow. Our transformation isn’t just external; it’s an internal shift in how and why we craft our mouthpieces. We’re thrilled for what’s ahead. Follow us on social media to be part of this storied legacy and the exciting new chapter we’re creating.
-
Critics have mentioned inconsistency in tip openings for Meyer and Otto Link mouthpieces. Why is that?
We fully acknowledge that there was truth to this critique in the past. For too long, JJ Babbitt’s inattention to detail in this area led to inconsistent tip openings, which affected the trust musicians placed in our products. We didn’t respond to feedback as we should have, and it was a flaw in our approach.
However, in this new season, starting in 2020 and continuing today, we’ve radically tightened our processes and tolerances. We’ve implemented precise methods to ensure far greater consistency across our mouthpieces, without losing the handcrafted individuality that sets them apart. This commitment to transparency and quality has been at the heart of our transformation.
At JJ Babbitt, we use finely calibrated digital gauges with built-in backstops to ensure precise and consistent tip opening measurements. Every mouthpiece is measured from a fixed reference point—the very front of the outside tip rail opening—and goes through multiple quality checks to confirm accuracy.
If your personal measurements don’t match our specifications, several factors could be at play:
Measurement Point Differences: Even a slight shift in where the measurement is taken along the tip rail can change the reading by several thousandths of an inch.
Gauge Variations: Many personal gauges lack a fixed backstop, making positioning inconsistent and leading to measurement discrepancies.
Technique Factors: Hand positioning, gauge angle, and pressure applied during measurement can all affect the final result.
We understand how important tip opening accuracy is to musicians, and we take it seriously. If you haven’t tried a Meyer or Otto Link mouthpiece recently, we invite you to experience the improvements firsthand—we believe you’ll notice the difference.
-
I've heard that JJ Babbitt's mouthpieces don't measure up to their advertised specifications, especially when checked with personal gauges. How does the company ensure accuracy in tip openings and other critical dimensions?
As musicians, we all understand how even the smallest variations in a mouthpiece can influence feel and response. At JJ Babbitt, we take this responsibility seriously, ensuring that every mouthpiece is crafted with precision and consistency. Each piece is 100% handcrafted and, because of this, undergoes extensive quality control at multiple stages of production. We use finely calibrated, proprietary digital gauges and instruments to measure critical dimensions, including tip openings, to ensure that every mouthpiece aligns with our advertised specifications and falls within our established tolerances.
We recognize that players often take an active interest in measuring their equipment, and while personal gauges—whether digital or analog—can be useful tools, they may introduce unintended variables. Differences in measuring techniques, slight changes in positioning, or even the pressure applied during freehand measurement can all contribute to discrepancies.
The most common cause of inaccurate readings compared to our advertised measurements is that most personal gauges lack a “backstop”—a fixed position that ensures each mouthpiece is measured from the exact same spot every time. Without this absolute positioning, even the slightest shift in placement can affect the reading.
Where the gauge contacts the tip rail makes a significant difference. While the distance may seem minor, a measurement taken at the very front of the tip rail versus the back can vary by several thousandths of an inch—especially on larger tip openings. Our proprietary gauges, designed with a built-in backstop, eliminate this inconsistency by ensuring that every mouthpiece is measured from the same exact point on the tip rail—something that is extremely difficult to replicate freehand with third-party gauges.
Unfortunately, some have concluded—and even perpetuated the belief—that we at JJ Babbitt “don’t care” about details like this. Nothing could be further from the truth. We deeply respect the attention to detail that musicians bring to their craft, and we’re always happy to have conversations about the measurement process and the factors that contribute to perceived differences.
Our goal is to ensure that every player gets the best experience possible with a mouthpiece that is measured, checked, and verified with the highest level of accuracy before it leaves our workshop.
-
Why isn’t the table on a Meyer, Otto Link, or Hite mouthpiece perfectly flat? Can’t you just make them flat?
This is a great question and one we hear often. It’s easy to assume that a perfectly flat table would be ideal or that the handcrafted nature of our mouthpieces means we’re unable to achieve that precision. The reality, however, is far more intentional and deeply rooted in history.
We absolutely have the capability to make the tables perfectly flat—but we choose not to. The Meyer brothers and Otto Link believed that a slight concavity, often referred to as a “belly,” enhances the seal between the reed and mouthpiece, contributing to a richer, more responsive tone. This design philosophy has shaped the playing experience of generations of musicians, and we continue to uphold it today.
That said, we recognize that at times in our history, even a well-intended design choice wasn’t always regulated with the consistency it required. Handcrafted work naturally introduces some variability, but that variance should never be extreme. We’ve worked diligently to refine our quality control processes, ensuring that the concavity remains intentional and precise—enhancing performance rather than hindering it. A defining feature should never become a flaw, and we take great care to uphold the legacy of these mouthpieces while maintaining the highest standards of craftsmanship.
Ultimately, this subtle but significant design element is part of what makes Meyer, Otto Link, and Hite mouthpieces unique. It’s a hallmark of tradition that allows musicians to create a sound that’s as distinctive as they are—while ensuring that the quality remains as reliable as the design philosophy itself.
-
I've heard people talk about the 'Otto Link Lottery'—that some Otto Link mouthpieces play differently from one to the next. Is that true?
The “Otto Link Lottery” is a real part of our history, and we understand why. There have been seasons where our quality control wasn’t where it should have been. As players became more discerning—not just in what they heard but in what they saw—our hands didn’t always keep pace. That’s something we’ve taken to heart.
At JJ Babbitt, we’re proud of Otto Link’s legacy, but we’re even prouder of the advancements we’ve made in consistency while maintaining the handcrafted excellence that defines our mouthpieces. Over the past several years, we’ve refined every step of our process—tightening tolerances in manufacturing, improving our hand-finishing consistency, and strengthening final inspections.
The result? Otto Link mouthpieces that uphold the legendary sound and feel players love—but now with a level of reliability that ensures every piece is worthy of the name. Each mouthpiece is still handcrafted, and every musician will connect with theirs in a unique way. But today, you don’t have to search through a dozen Otto Links to find a great one. Every Otto Link we ship is made to be great.
-
What is the line on the chamber floor and/or body of Otto Link metal mouthpieces? Is it a crack?
The line you see is not a flaw but a signature feature of our manufacturing process. Metal Otto Link mouthpieces are forged from two halves, then brazed together—a proprietary method dating back to Otto Link himself. This seam, or 'witness line,' is the result of joining the two halves, contributing to the unique tonal qualities of our mouthpieces.
-
Do molded and vulcanized hard rubber mouthpieces like Meyer and Otto Link sound different from those made from extruded rubber rod (CNC) or 3D printed from plastic filament?
Absolutely, yes. While players may or may not prefer the tonal differences that result from our process, there is no denying that the differences are there, and they are intentional. The material and the process set our mouthpieces apart, contributing to the warmth and depth of tone that define Meyer and Otto Link. There’s a bit more detail about that on our Handcrafting Page if you want to learn more. Competitors may replicate dimensions, but they can’t capture the full character shaped by our unique methods and materials.
-
Is today’s rubber as good as what was used in the 1930s, 40s, and 50s?
Absolutely. The natural rubber we use is sourced from the same organic origins as they always have been. While regulatory changes have altered some processing elements, our rubber retains its quality. The handcrafted blending and post-mold vulcanization are features of our process that ensure the same quality mouthpieces we’ve always produced.
-
Does silver soldering and high-temperature brazing on metal mouthpieces affect the sound and personality of a metal mouthpiece?
Yes, it does. Brazing not only joins the two halves of the mouthpiece but also anneals the brass, causing metallurgical changes at the molecular level. This process enhances the tonal warmth and creates a unique playing personality that sets our mouthpieces apart from CNC-manufactured mouthpieces made from metal bar stock. The combination of this handcrafted technique and metallurgical precision contributes to the rich, resonant sound that defines our metal mouthpieces.
-
Does JJ Babbitt manufacture Meyer and Otto Link mouthpieces differently than Frank and Ed Meyer, Otto Link, or Ben Harrod did?
Not at all. Our handcrafted process is still a defining feature, carried forward from generation to generation. Our mouthpieces are made the way they’ve always been made, with the passion, intentionality, skill, and craftsmanship of our people being the key ingredients.
-
JJ Babbitt’s handcrafted rubber and metal mouthpieces are less expensive than many competitors' automated pieces. Why is that?
We’ve always believed that high-quality mouthpieces should be within reach for as many musicians as possible. Achieving great sound shouldn’t be dependent on the depth of your wallet. In the broader world, handcrafted work typically demands a higher price point, and while we could adjust our pricing because of this, we choose not to. Our handcrafted process allows us to offer exceptional pieces at an accessible price point. While other brands have inflated their prices considerably, Meyer and Otto Link have remained a great value for players.
-
Some have said JJ Babbitt was a 'closed shop' and didn’t listen to feedback or connect with players, artists, educators, or retailers. Has that changed?
Absolutely. Since the Rorie Family took over in 2021, connecting with musicians, artists, and educators has not only become a top priority—it’s a hallmark of what we love. We actively listen to feedback and closely watch musical and playing trends to ensure we’re serving the community in meaningful ways. To be a part of this community, you can follow us on Instagram, Facebook, and YouTube—links to our social channels are located at the top and bottom of this website. You can also reach out to us any time at info@jjbabbit.com.
-
Many modern players prefer brighter, louder mouthpieces. Does JJ Babbitt offer models for them?
Yes, and we’ve embraced this desire in several of our mouthpieces. We recommend trying the Meyer Bros Connoisseur Series or the new Otto Link LA hard rubber Tenor. Both are designed for greater projection and brightness, without losing the nuanced tone Meyer and Otto Link are known for.
-
The Slant Sig Otto Link tenor mouthpiece is often copied. Do you still offer it?
Yes, although we’ve rebranded it as the Otto Link Vintage. The Vintage retains all the core features that made the Slant Signature so legendary—a dark, buttery-smooth tone for tenor players seeking a rich sound.
-
Can I have my Meyer or Otto Link mouthpiece refaced at the factory?
Yes! What was once unavailable is now a valuable feature of our service. We offer refacing for Meyer or Otto Link mouthpieces through the JJ Babbitt Custom Shop, which operates seasonally. For more details, visit the JJ Babbitt Custom Shop page on this website.
-
Can I visit JJ Babbitt for a tour and mouthpiece trial?
Absolutely! We love having musicians visit the workshop to witness our handcrafting process up close. Visitors consistently leave with a deep sense of admiration for the craftsmanship and a greater appreciation for how we’ve preserved time-honored mouthpiece crafting techniques while embracing modern technology. You can also play-test our latest models. It’s an experience every mouthpiece enthusiast shouldn’t miss. While we don’t sell directly, we can coordinate your purchase with your preferred retailer.
-
What role does the baffle play in the sound and feel of a jazz mouthpiece?
The baffle shape and size are key features that control the airflow and directly influence the mouthpiece’s sound. Higher, convex baffles act like ramps, creating a brighter, more projected sound. Lower or scooped baffles, on the other hand, produce a darker, mellower tone. While some may see the baffle design as rigid, it’s actually tailored for different playing styles, and your embouchure and oral cavity play a role in the overall experience.
-
What role does vulcanization play in making hard rubber mouthpieces?
Vulcanization transforms a soft, flexible rubber piece into the durable, dense mouthpiece musicians expect from Meyer and Otto Link. This process is crucial to ensuring the richness and consistency of our mouthpieces, across both vintage and modern eras.
-
Why do some older rubber mouthpieces turn brown over time?
Over time, exposure to sunlight, humidity, and cleaning methods can cause variations in color. Each mouthpiece ages differently, depending on the natural variations in the rubber and how it has been maintained.