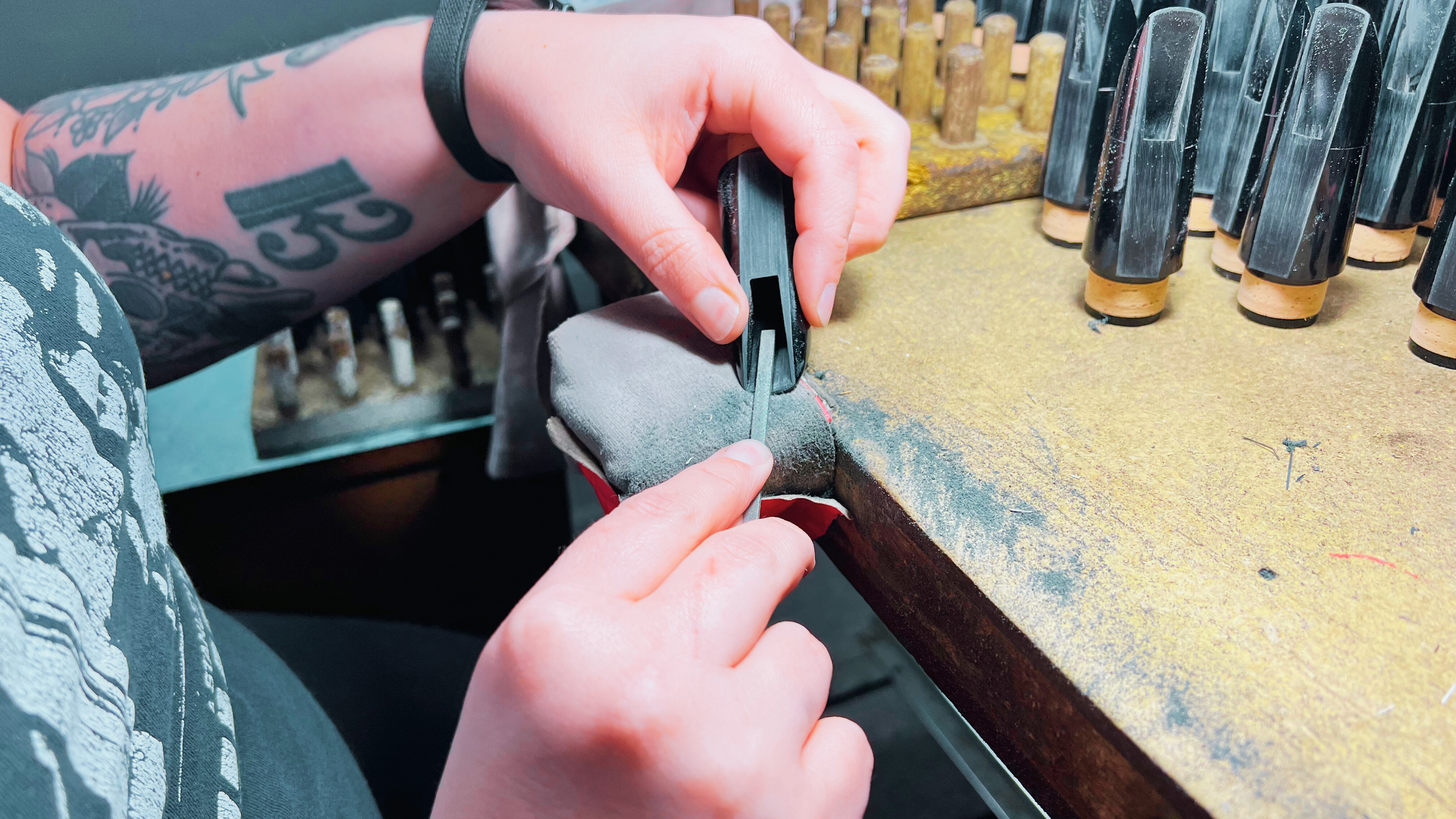
"Every handcrafted piece carries the soul of its creator, a reflection of their artistry, a testament to their passion, and a legacy that echoes through every note."
A Mouthpiece as Unique as You
At JJ Babbitt, we believe that no two musicians are the same, and their mouthpieces shouldn’t be either. Our 100% handcrafted approach allows us to celebrate the individuality of each player, creating pieces that aren’t just manufactured or mass produced—they’re brought to life with a touch that only skilled hands can deliver. It’s not about uniformity; it’s about crafting something as unique as the artists who play them.
In our workshop, the creation of each mouthpiece is where tradition meets modern craftsmanship, bridging over a century of artistry with the exactness required by today’s musicians. Every piece is meticulously shaped by skilled hands, guided by generations of expertise, and infused with purpose at every step. This process is not simply manufacturing—it’s an art form, where every cut, grind, and polish is dedicated to bringing each mouthpiece to life.
Our hard rubber mouthpieces begin with a specially formulated natural rubber compound, carefully mixed to achieve an ideal balance of density and elasticity. This compound is then molded and undergoes an 18-24 hour vulcanization process, during which it is heated with other unique, proprietary elements to create resilient cross-links between the rubber molecules. This step doesn’t just harden and stabilize the material; it enhances its durability and tonal integrity by forming a dense, long-lasting structure. Once vulcanized, each mouthpiece is hand-shaped, hand-faced, and hand-finished to allow the natural tonal qualities of the material to shine through. The result is a sound that is warm, smooth, and rich in character—qualities that appeal to musicians across diverse styles and preferences.
Our process for metal mouthpieces is equally grounded in science and craftsmanship. Each mouthpiece begins as two separate halves, forged under intense heat and pressure to densify the metal’s structure, preparing it for optimal resonance and projection. These halves are then carefully brazed together with silver solder, creating a molecular bond that enhances the structural integrity and stability of the mouthpiece. The final annealing step uses controlled heating and cooling cycles to relieve internal stress within the metal, allowing it to vibrate freely. This process improves the mouthpiece’s tonal warmth, depth, and responsiveness. Each metal mouthpiece is then meticulously hand-shaped, hand-faced, and hand-finished to further refine these qualities before being plated in 24-karat gold, creating a piece that is both visually striking and sonically resonant.
We believe that true character emerges when raw materials are shaped by hand, with meticulous detail applied at every stage—from formulating and shaping to finishing—unlike methods that rely on standardized metal and rubber rods simply cut to form by machines. Our handcrafted approach combines precise design with a palette of tonal colors and nuances that only our unique handling and processing of materials can achieve—creating qualities in each mouthpiece that cannot be replicated by any other maker. While CNC machining focuses on repeatability and uniformity, our handcrafting process enhances the tonal complexity and responsive qualities of each mouthpiece, offering musicians a depth and warmth that go beyond structure alone. Each JJ Babbitt mouthpiece carries subtle, individual nuances that bring it to life, allowing players to explore a sound as unique and dynamic as their own musical identity.
This commitment to artistry has shaped the sounds of legends like John Coltrane, Stan Getz, Cannonball Adderley, Dexter Gordon, and more. Their voices were unmistakable, each one distinct, and our handcrafted mouthpieces continue this legacy of individuality. We believe that each musician deserves a mouthpiece that lets them express their own unique voice, allowing each mouthpiece’s natural nuances to shine through.
For musicians who seek to discover and express their own unique voice, our mouthpieces are crafted with that journey in mind. There’s a transformative moment when a musician finds a mouthpiece that not only feels right but unlocks their true voice, allowing them to communicate something personal and powerful. We create our mouthpieces to honor that moment, helping musicians celebrate and share their unique identity through sound.
At JJ Babbitt, mouthpieces are not merely products—they are the result of a journey of artistry and dedication. For those who value character over conformity and individuality over uniformity, our handcrafted mouthpieces offer a distinct path. This is the artistry we’ve honed for over 100 years, bringing together legacy, craftsmanship, and the singular voice of every musician who dares to stand out.
-
Our handcrafted mouthpieces are created through a detailed, hands-on process that includes forging, brazing, annealing, and for hard rubber, mixing, molding, and vulcanizing. This approach enhances tonal complexity and responsiveness, allowing each mouthpiece to develop a warm, nuanced sound with unique character. In contrast, CNC-made mouthpieces focus on repeatability and uniformity, using automated machines to cut standard rubber or metal rods to consistent dimensions. While CNC methods offer a high degree of uniformity, our handcrafted approach combines both accuracy in design and a unique “palette” of tonal colors and responsive nuances that can only be achieved through skilled, hands-on craftsmanship. This allows each JJ Babbitt mouthpiece to bring out the unique voice of each musician. Ultimately, it comes down to the personal preferences and playing style of each musician, with both approaches offering different experiences.
-
Accuracy is central to our process, especially in this new season at JJ Babbitt, and we achieve it through meticulous craftsmanship at every stage—but we’ll admit, it’s not easy! Without relying on machines to automate the work, each mouthpiece is carefully measured, shaped, and finished by hand to meet exact design specifications, allowing us to create mouthpieces with both structural accuracy and tonal complexity. By using detailed, hands-on techniques, our artisans introduce subtle tonal nuances that go beyond the uniformity of automated processes. Some musicians find this individualized character aligns with their playing style, while others may prefer the repeatability and uniformity offered by CNC production. Each offers a distinct experience, and the choice ultimately depends on the musician’s personal preferences.
-
Our handcrafting process adds layers of tonal complexity and warmth to each mouthpiece. For example, the unique mixing, milling, and vulcanization process in our hard rubber mouthpieces creates a dense, resilient structure that yields a rich, smooth sound, while the annealing and brazing of our metal mouthpieces allow the metal to resonate freely, enhancing depth and responsiveness. Each mouthpiece is then hand-shaped, hand-faced, and hand-finished to further refine its unique tonal qualities, resulting in a sound that is warm, resonant, and dynamic—qualities musicians often describe as “alive.” This isn’t just “marketing language”—it’s the science of acoustics at work. Through handcrafting, we’re applying physics to bring out the distinct character in every mouthpiece.
-
Handcrafted mouthpieces offer a unique character and depth that reflects the individual attention given to each piece. Our process refines each mouthpiece’s tonal qualities, enhancing warmth, responsiveness, and expressive range. For musicians seeking a mouthpiece that resonates with their personal voice, handcrafting brings an individualized quality that goes beyond the uniformity of machine-made methods, creating an intimate connection between the musician and their instrument. At the same time, CNC-made mouthpieces offer consistent, repeatable designs that some players may prefer for their unique characteristics and personality. Both approaches have their strengths, and the choice ultimately comes down to the musician’s individual style and preferences.
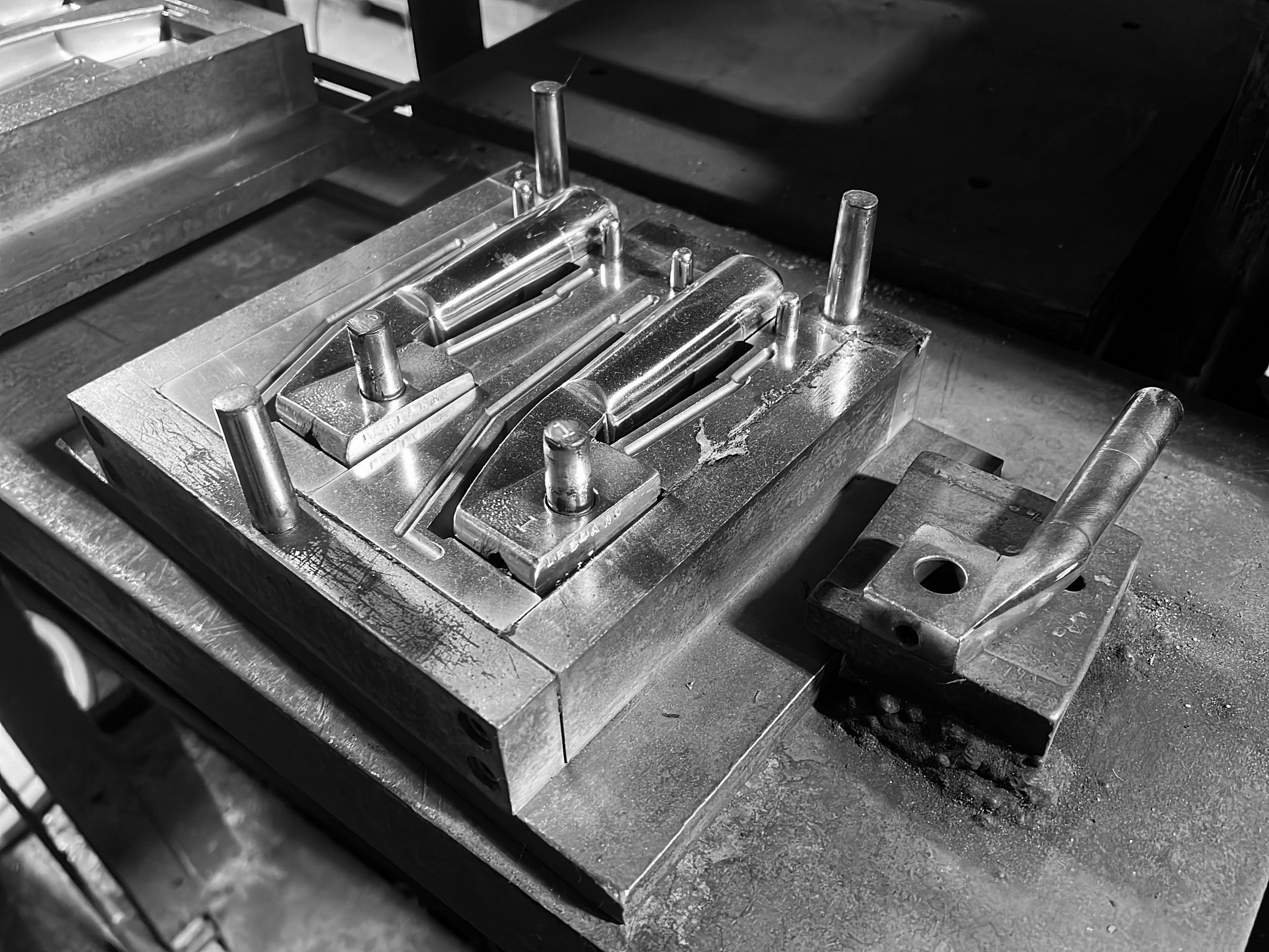
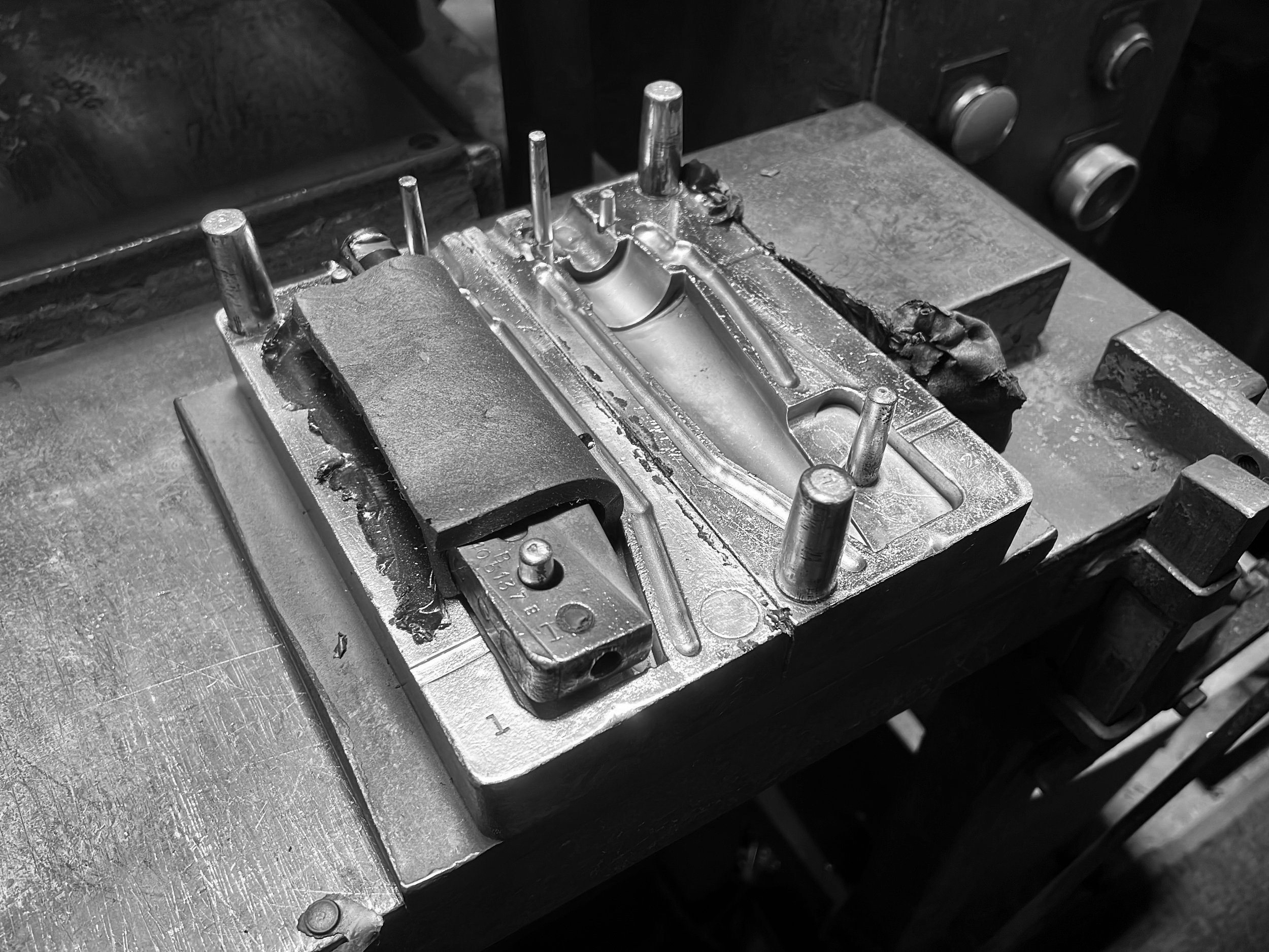
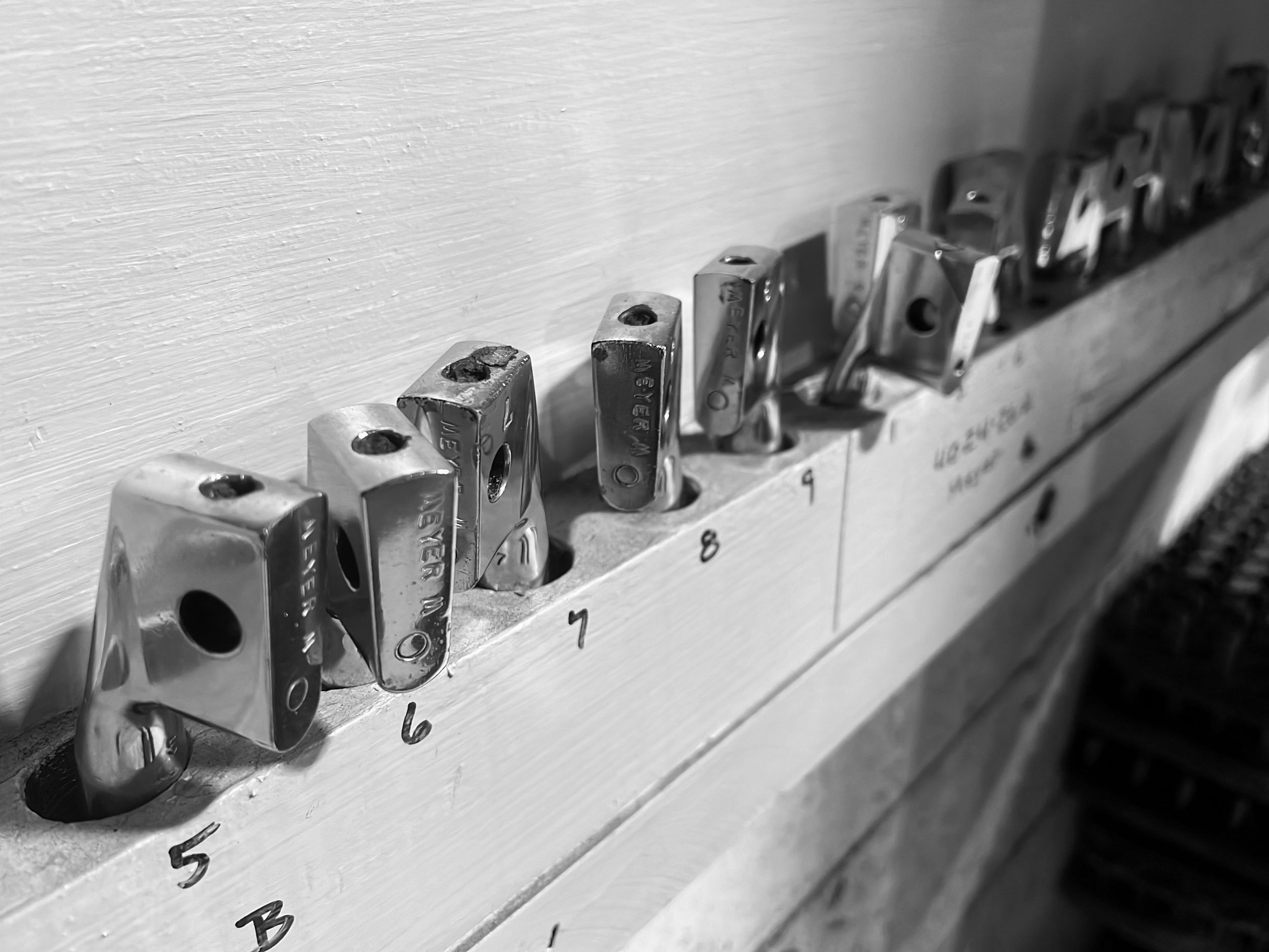
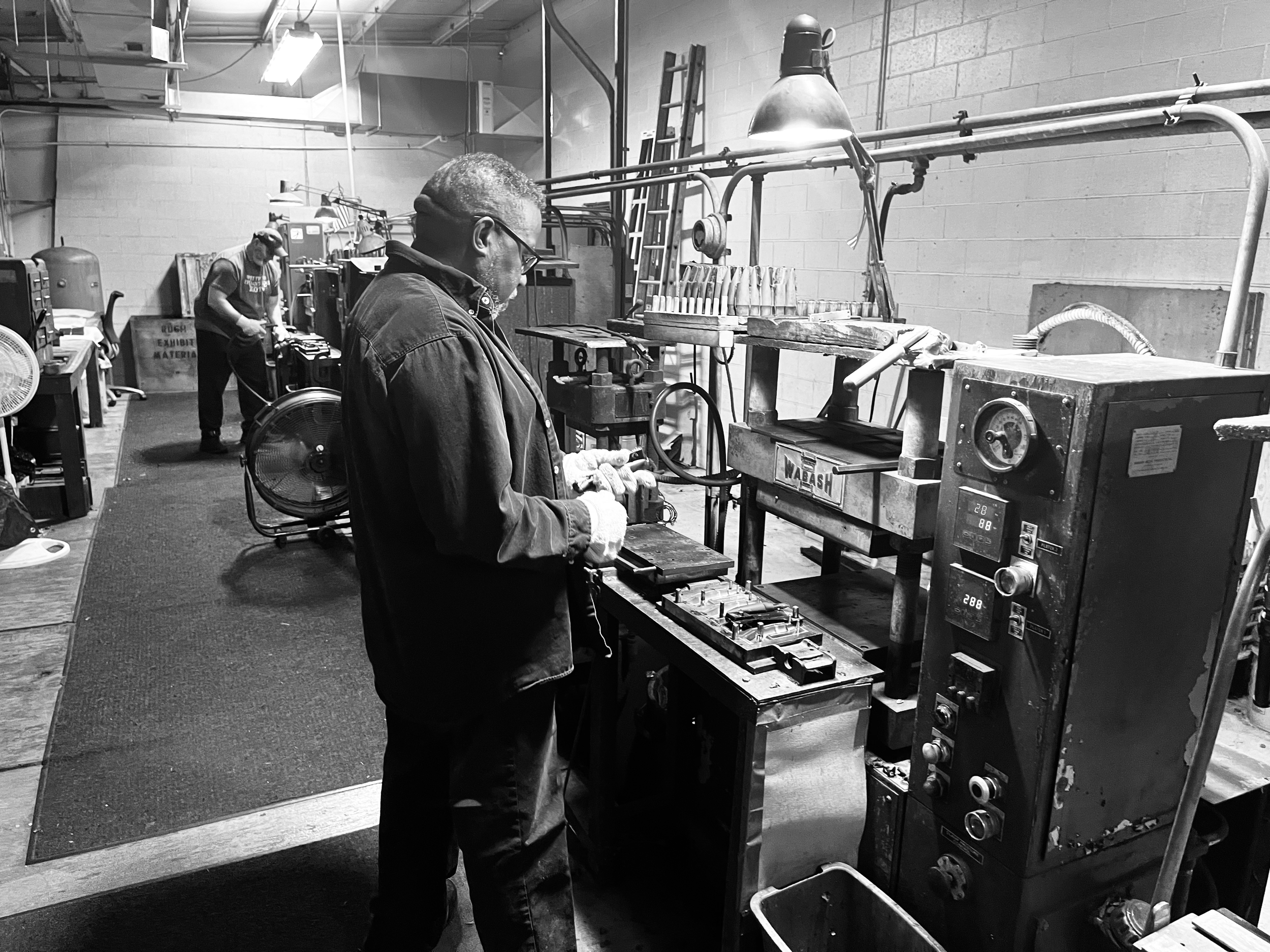
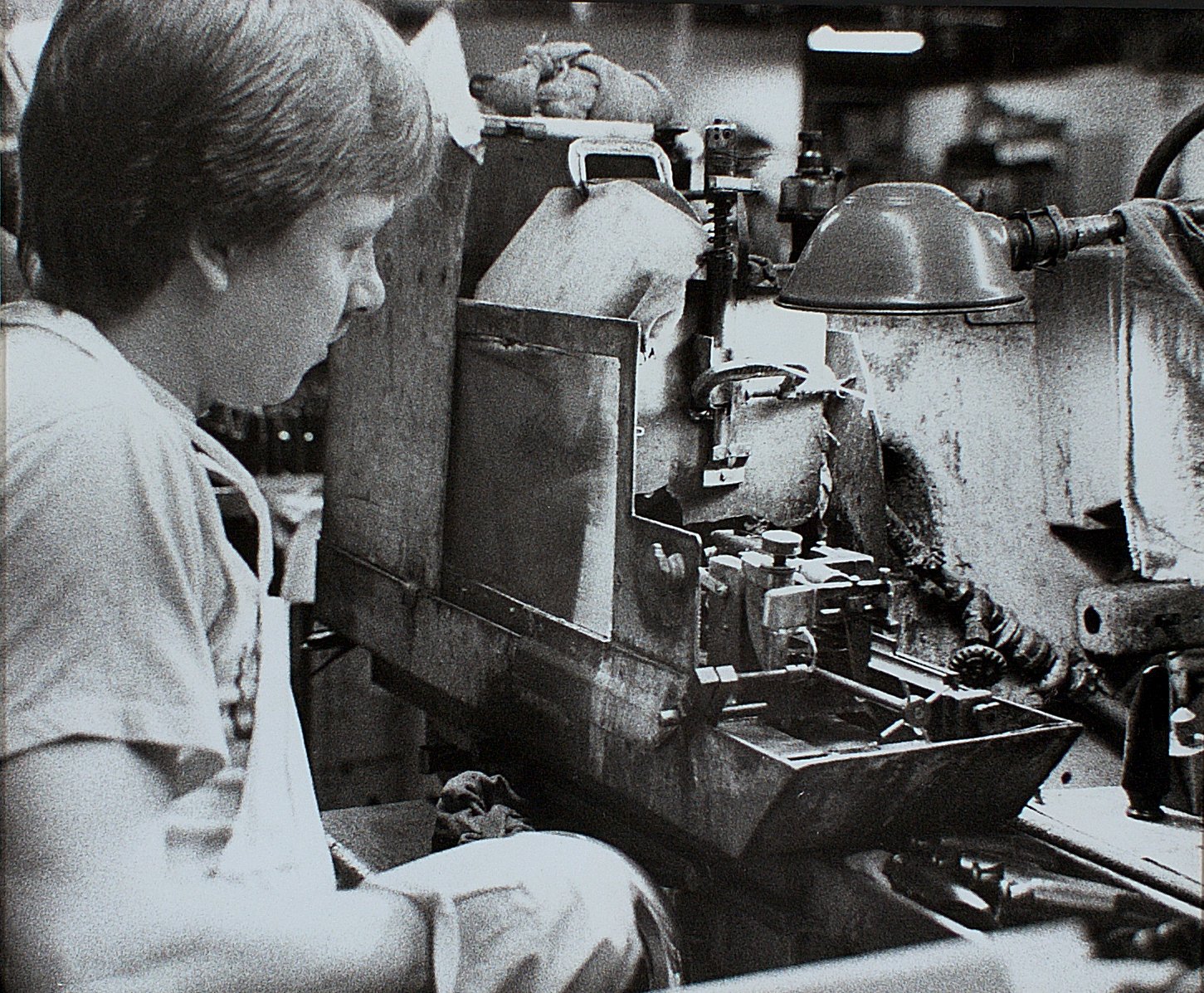
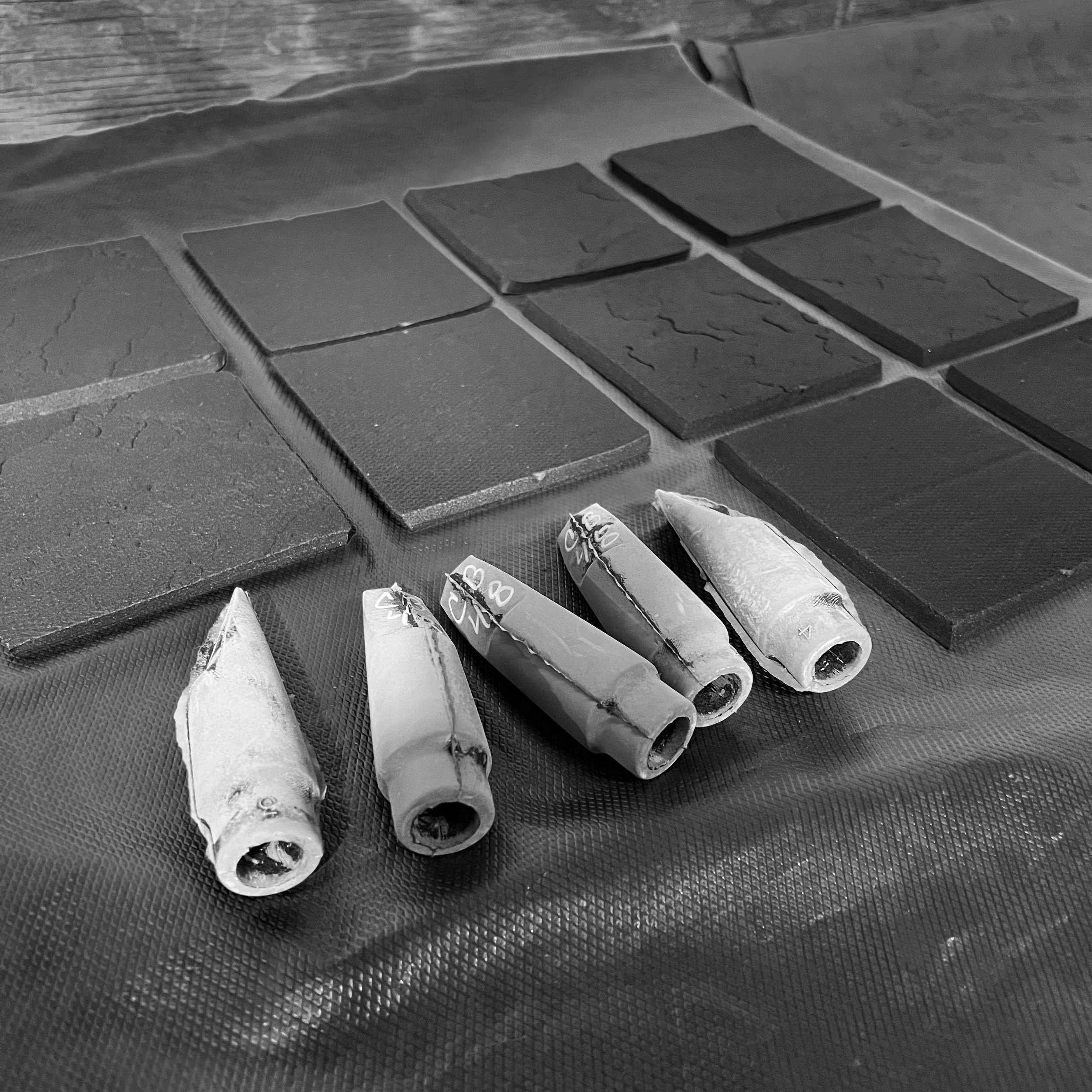
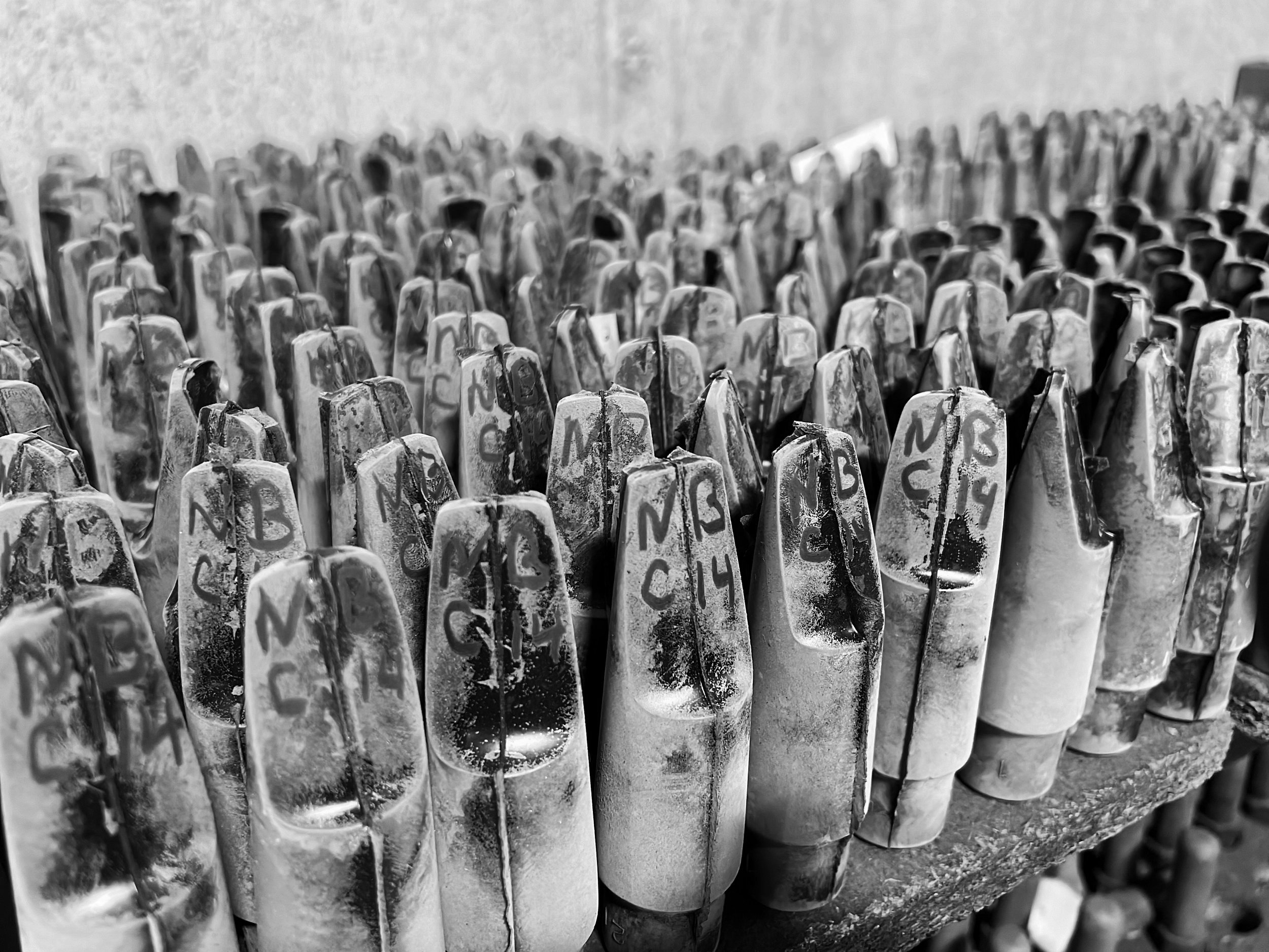
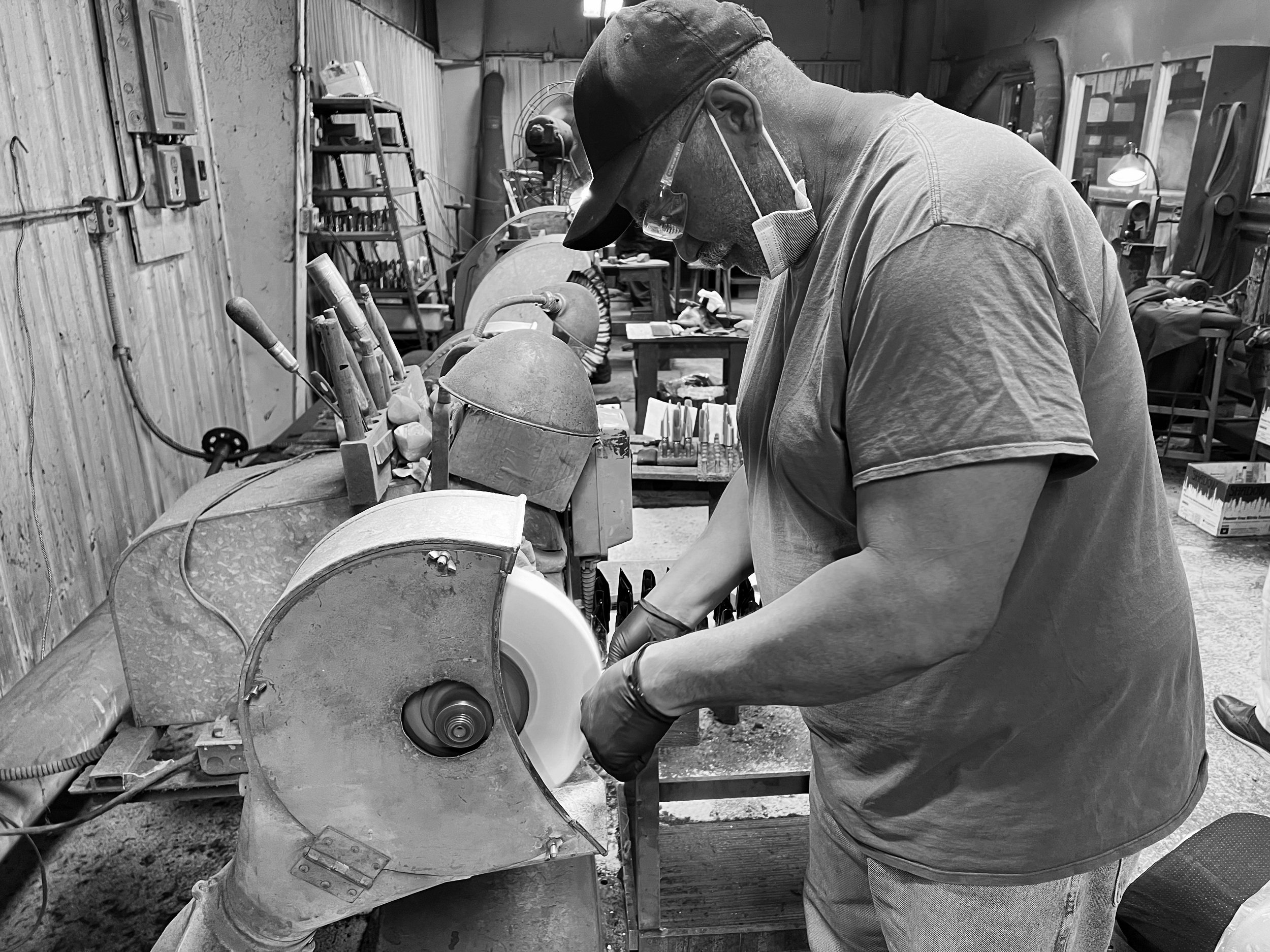
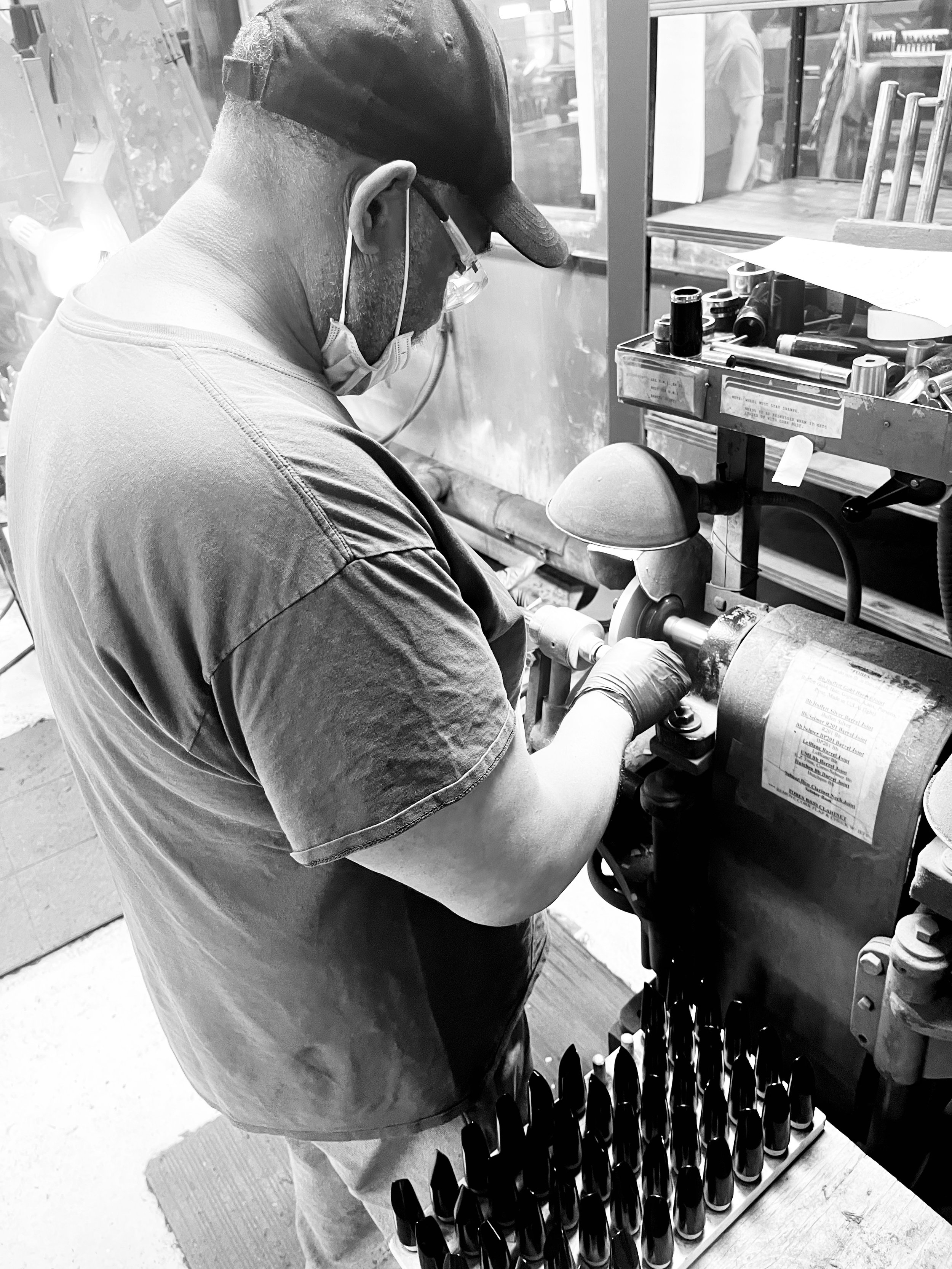

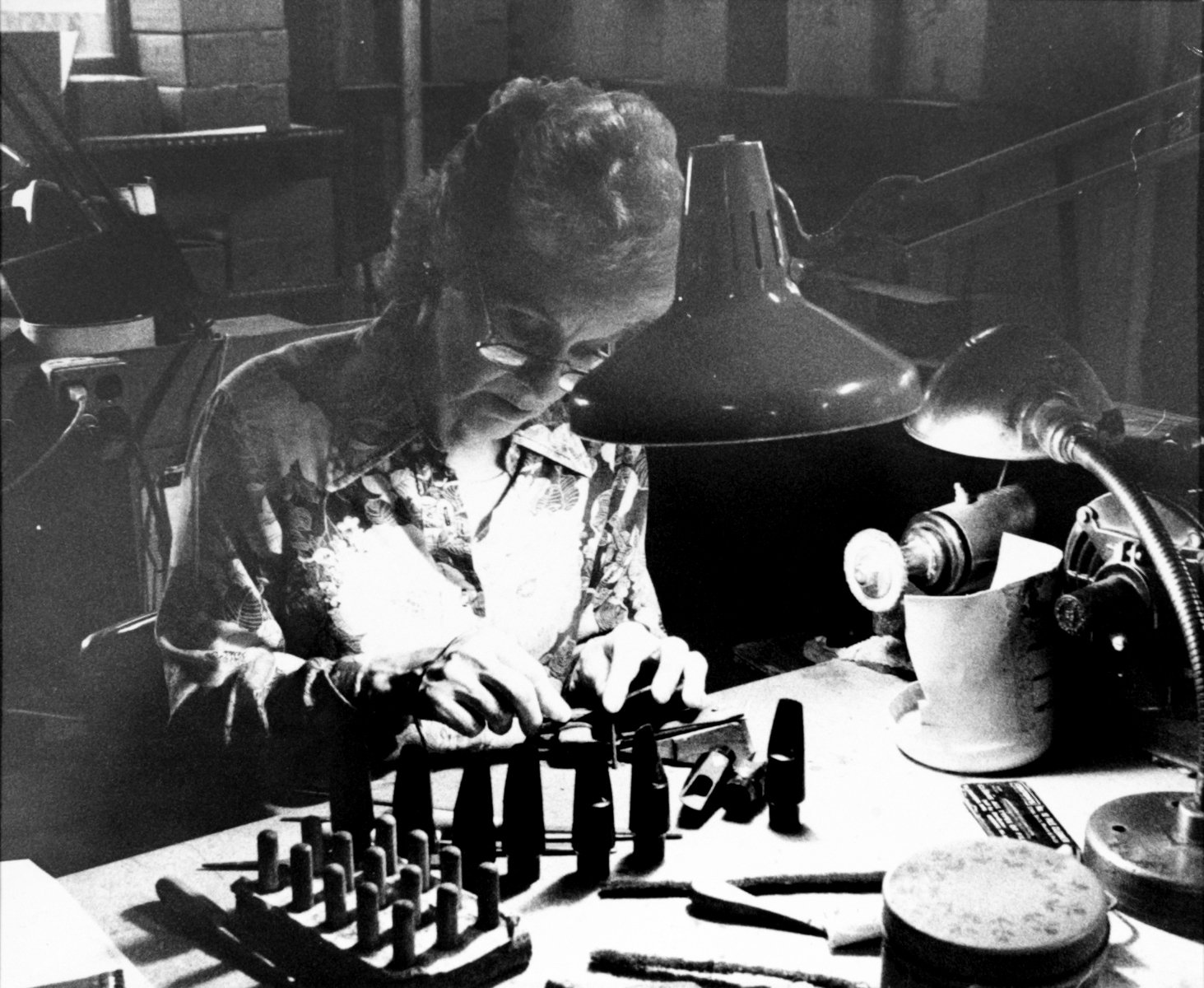
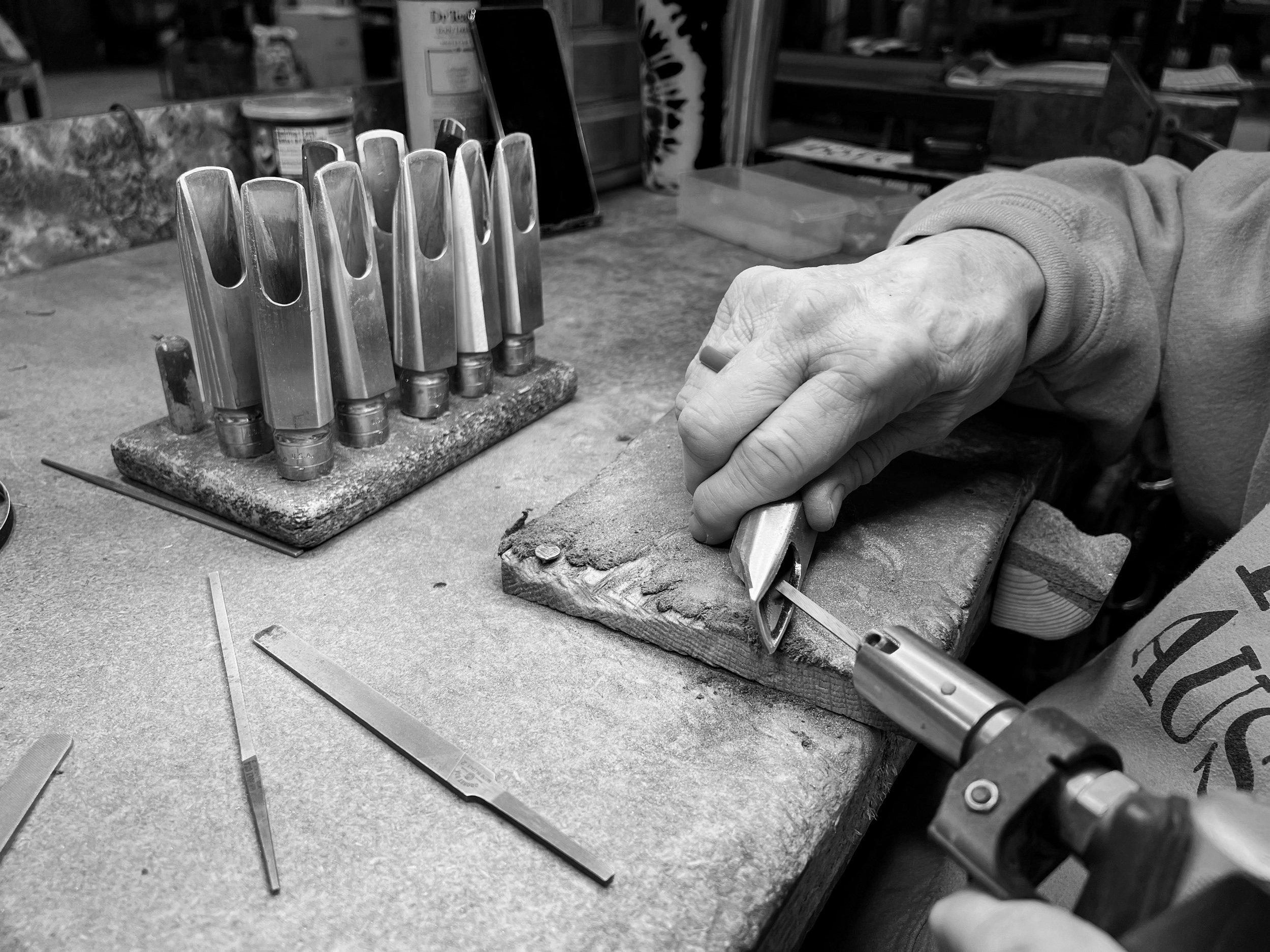
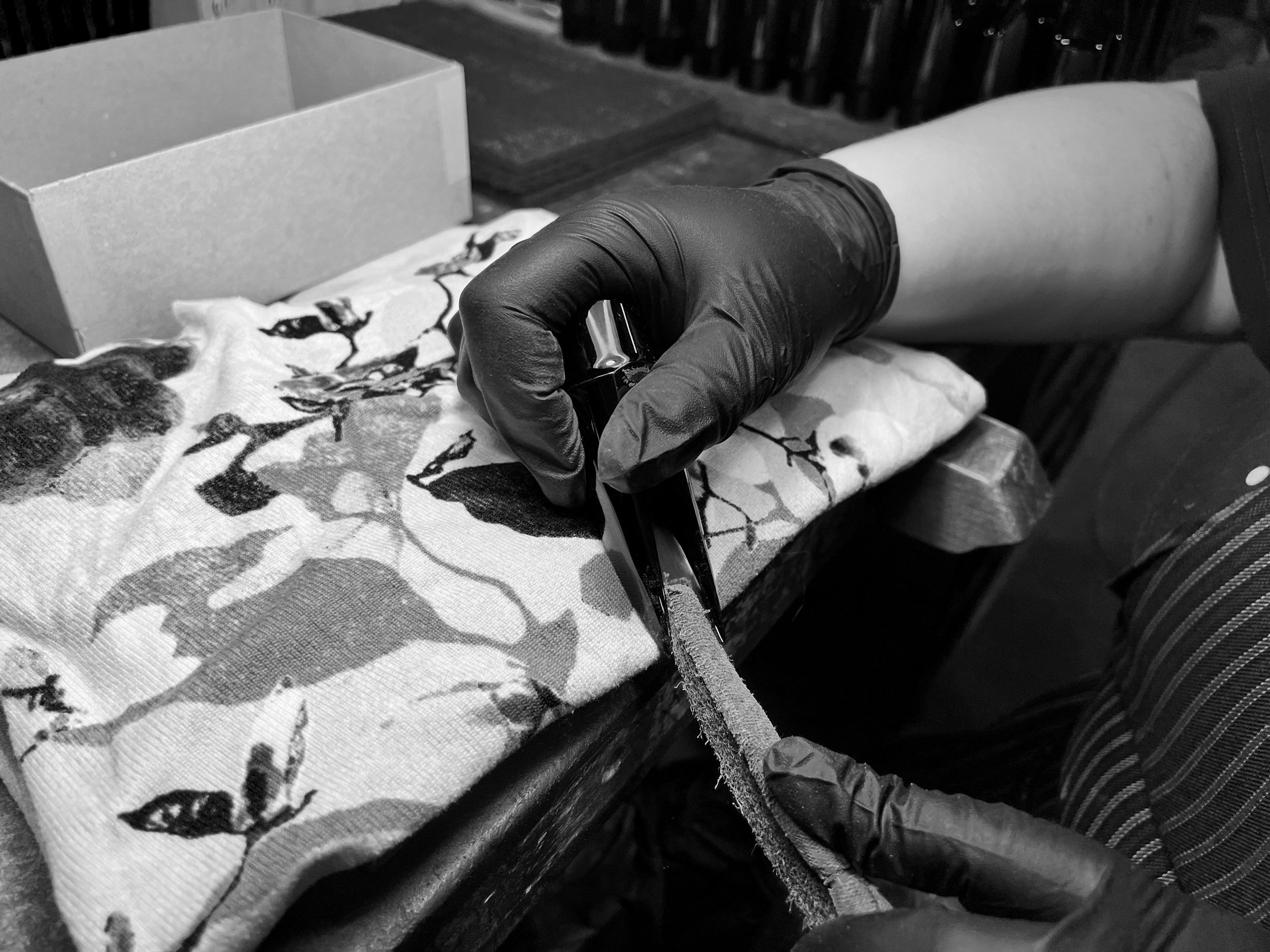

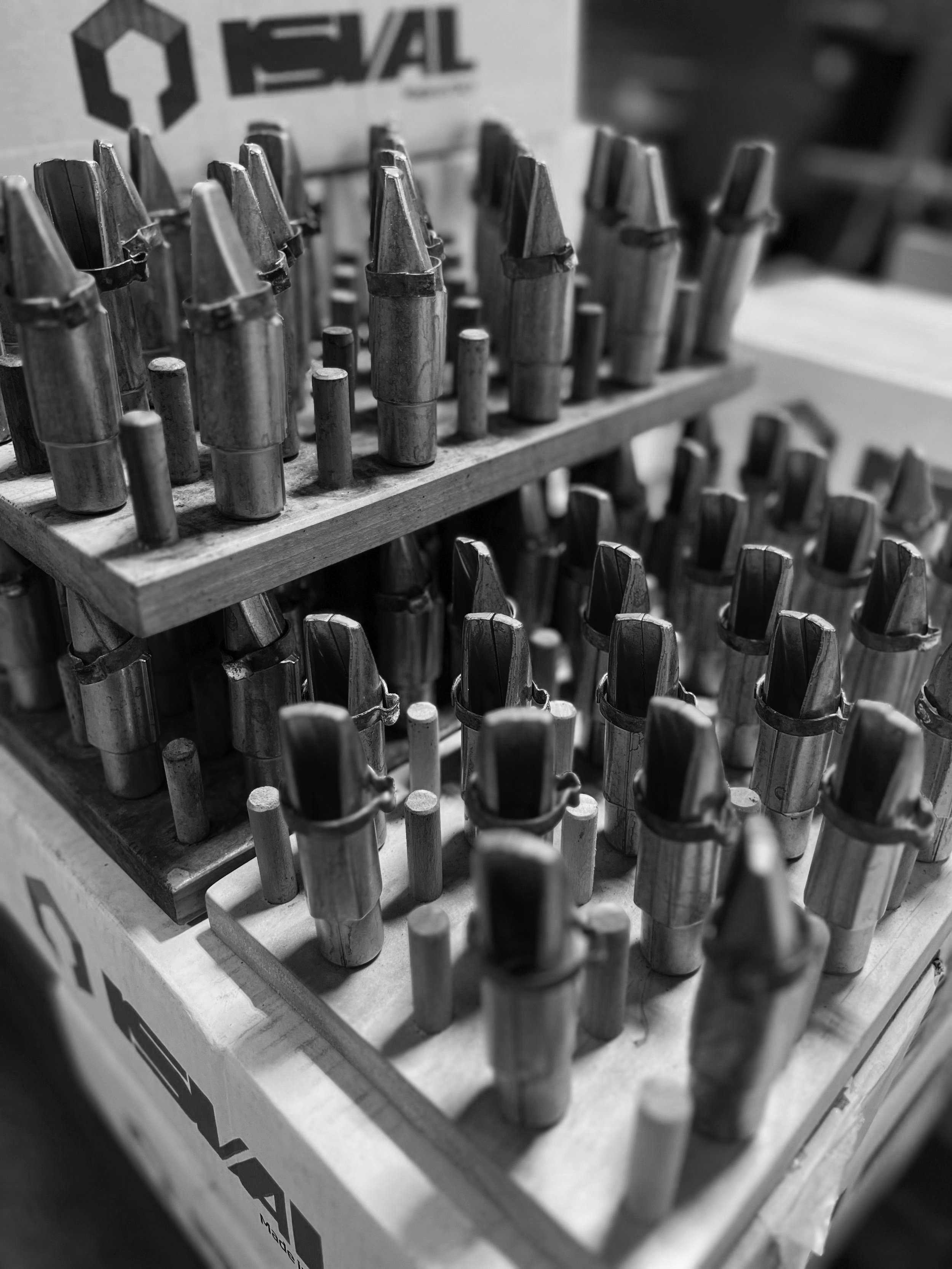
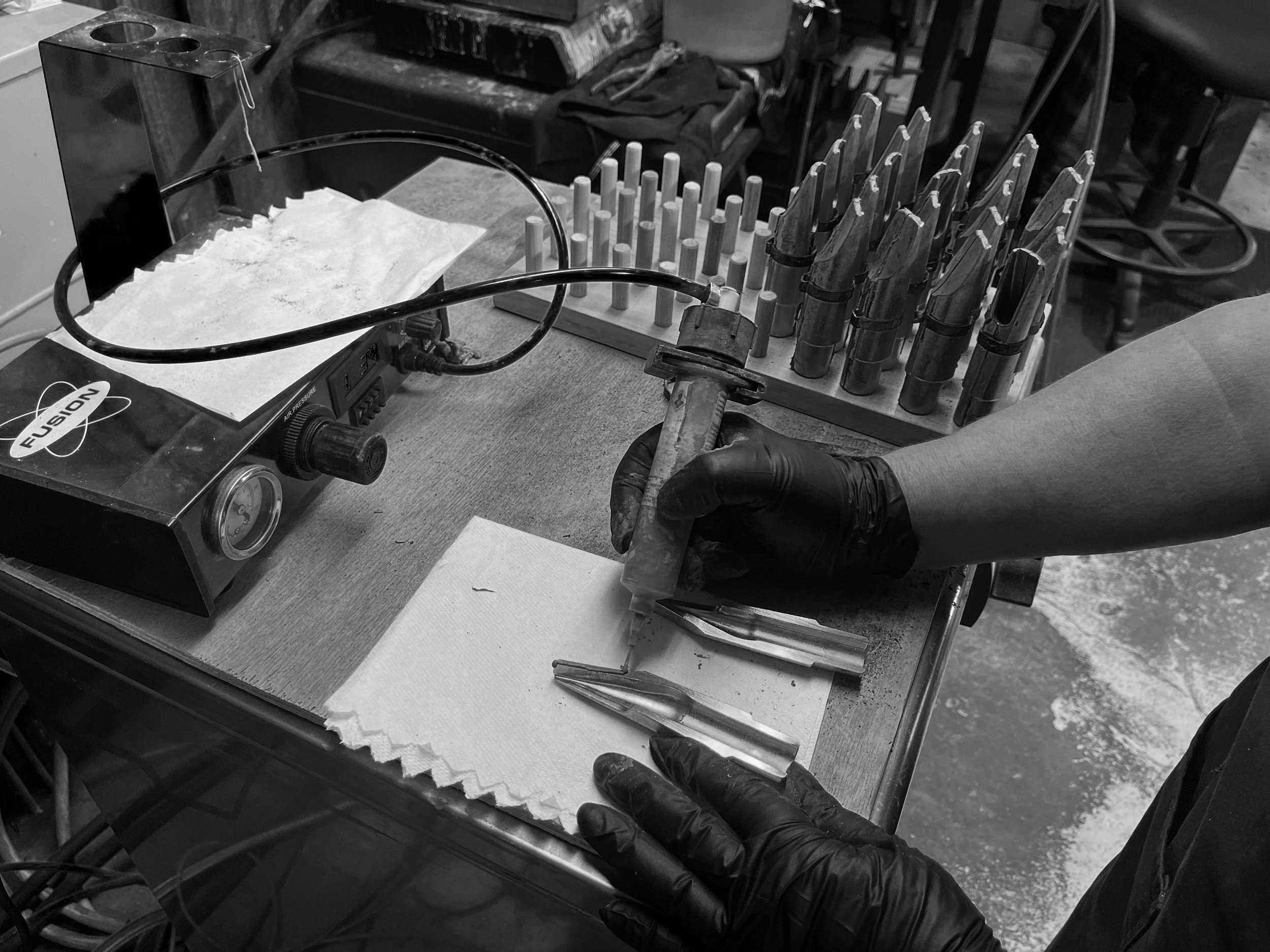
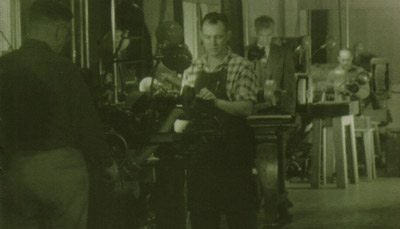

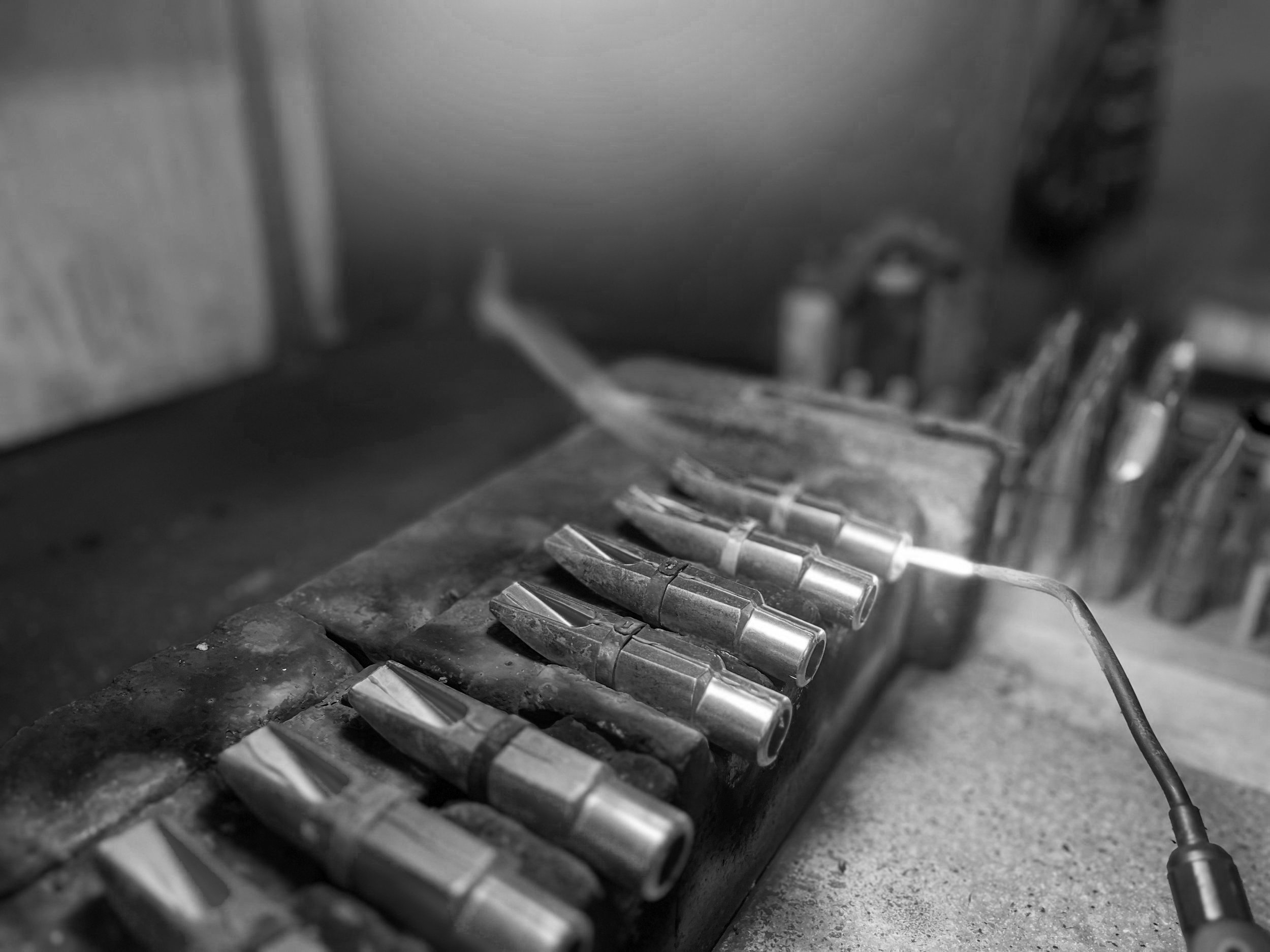
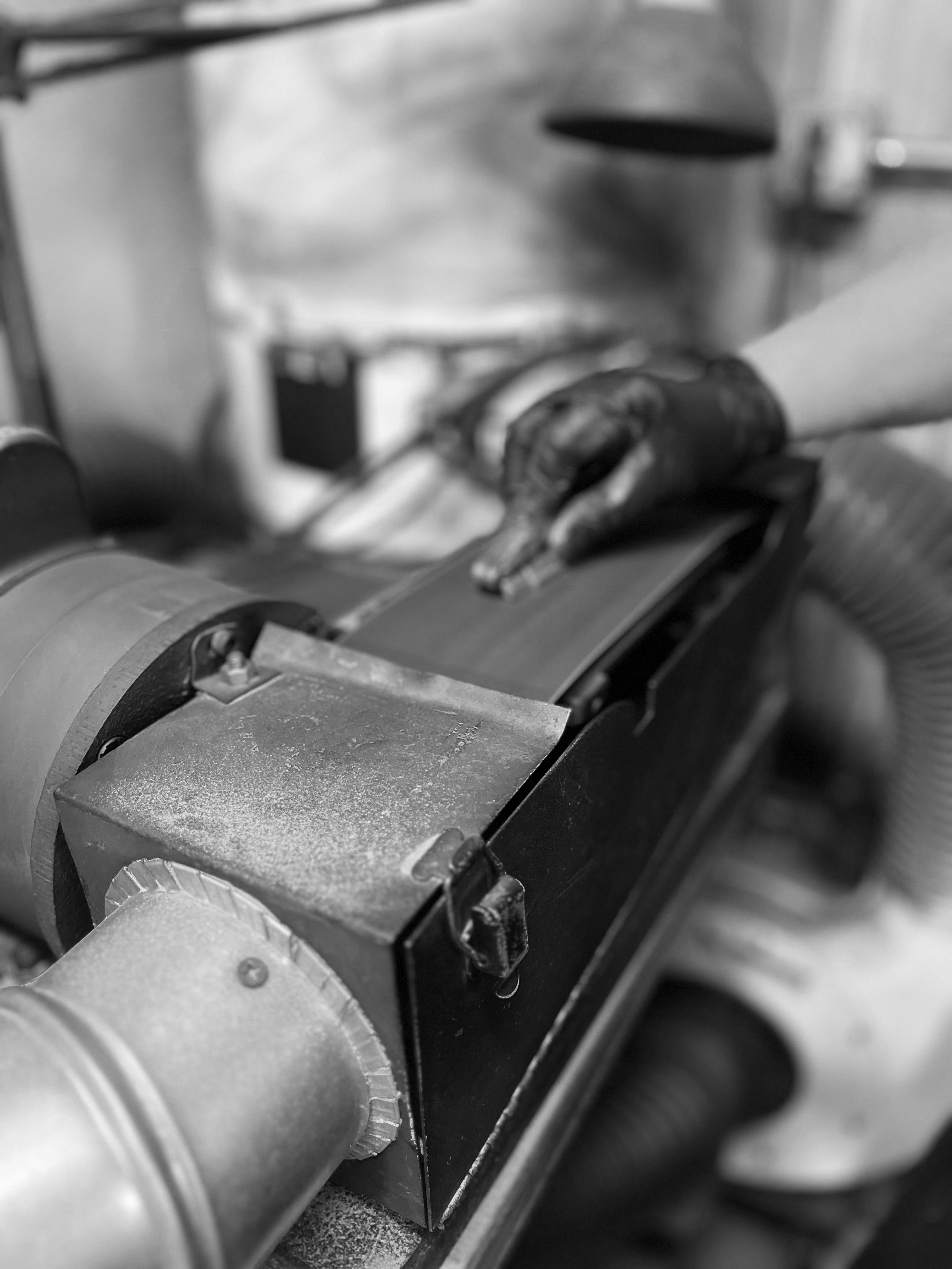
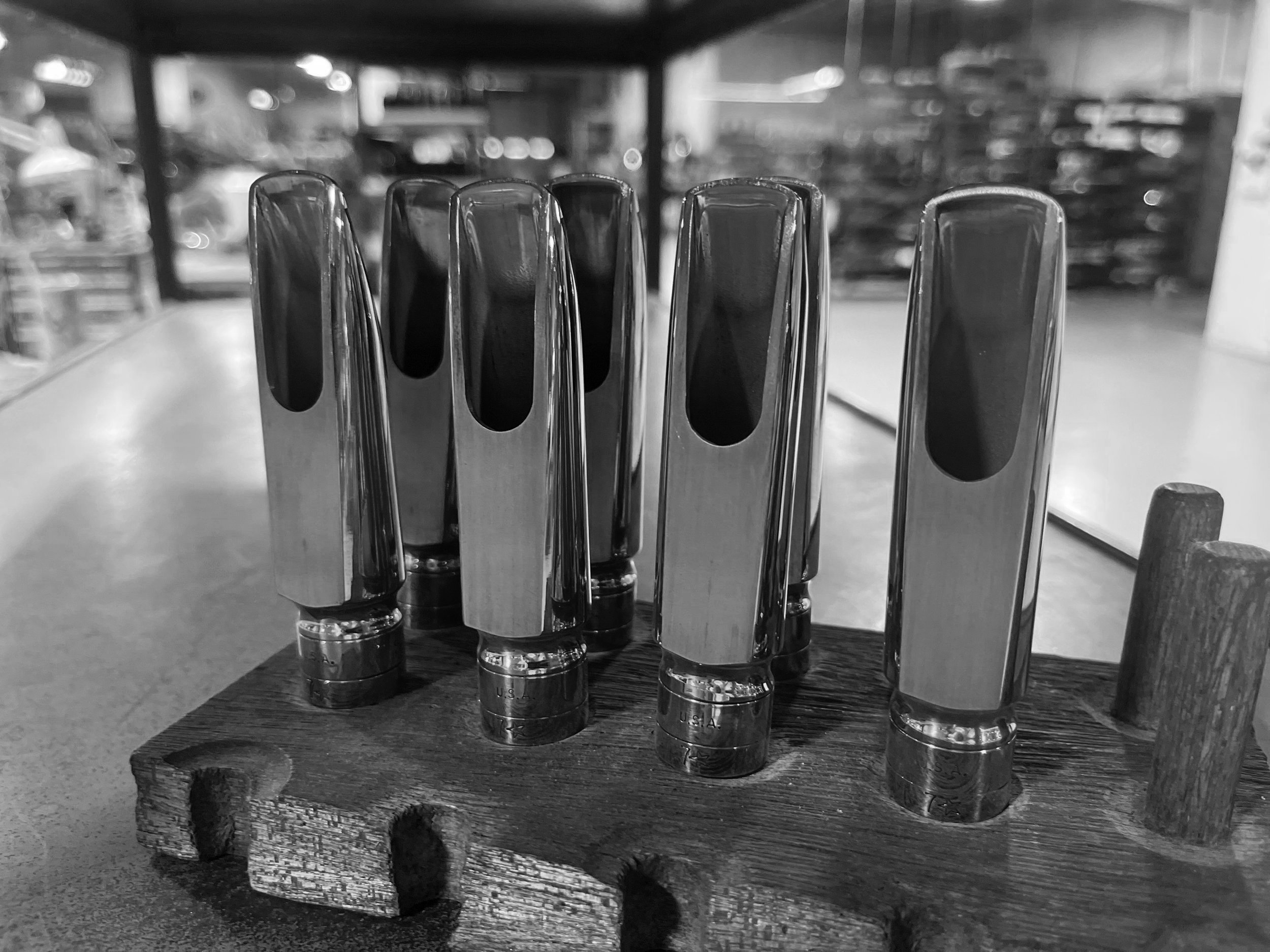